_TRAP: The Tyre Collective (202105)
www.thetyrecollective.com ︎︎︎
Every year 3.4 million tonnes of tyre particulate matter are produced, clogging our waterways and entering the air we breathe. Tyre-wear Recovery and Analysis Prototype (TRAP) lies at the intersection of innovation, design and engineering. It is the physical embodiment of a blue sky idea - that this otherwise lost waste stream can be harnessed for processing and reuse. My process was one of learning through making. Every decision has been based on experimental observation and computer modelling to produce the world’s first on-vehicle tyre wear capture device.

Fig. 1 TRAP our first on-vehicle working prototype
I plan to travel to Sweden with the rest of The Tyre Collective team this August, where we will rigorously test the device over 10,000km of driving. The samples we collect will be sent back to Prof. Frank Kelly and the Imperial Environmental Research Group for analysis - furthering scientific knowledge. I envisage a future where TRAP is ubiquitous throughout our cites. Together, we can make this future a reality, and save our air from tyre wear!

Fig. 2 A tyre wear particle under an electron microscope - the high surface area allows it to bind to toxins in the environment
No species has impacted our planet more than humanity. Exploding population coupled with burgeoning socioeconomic desires has fuelled unprecedented consumption and the generation of waste. Nothing highlights this more than the emergence of microplastic pollution. Until recently, very few people were aware of tyres being a source of microplastics.
TRAP: The Tyre Collective aims to mitigate emissions by capturing tyre wear at the source to ensure clean air, safeguarding our environment and health.

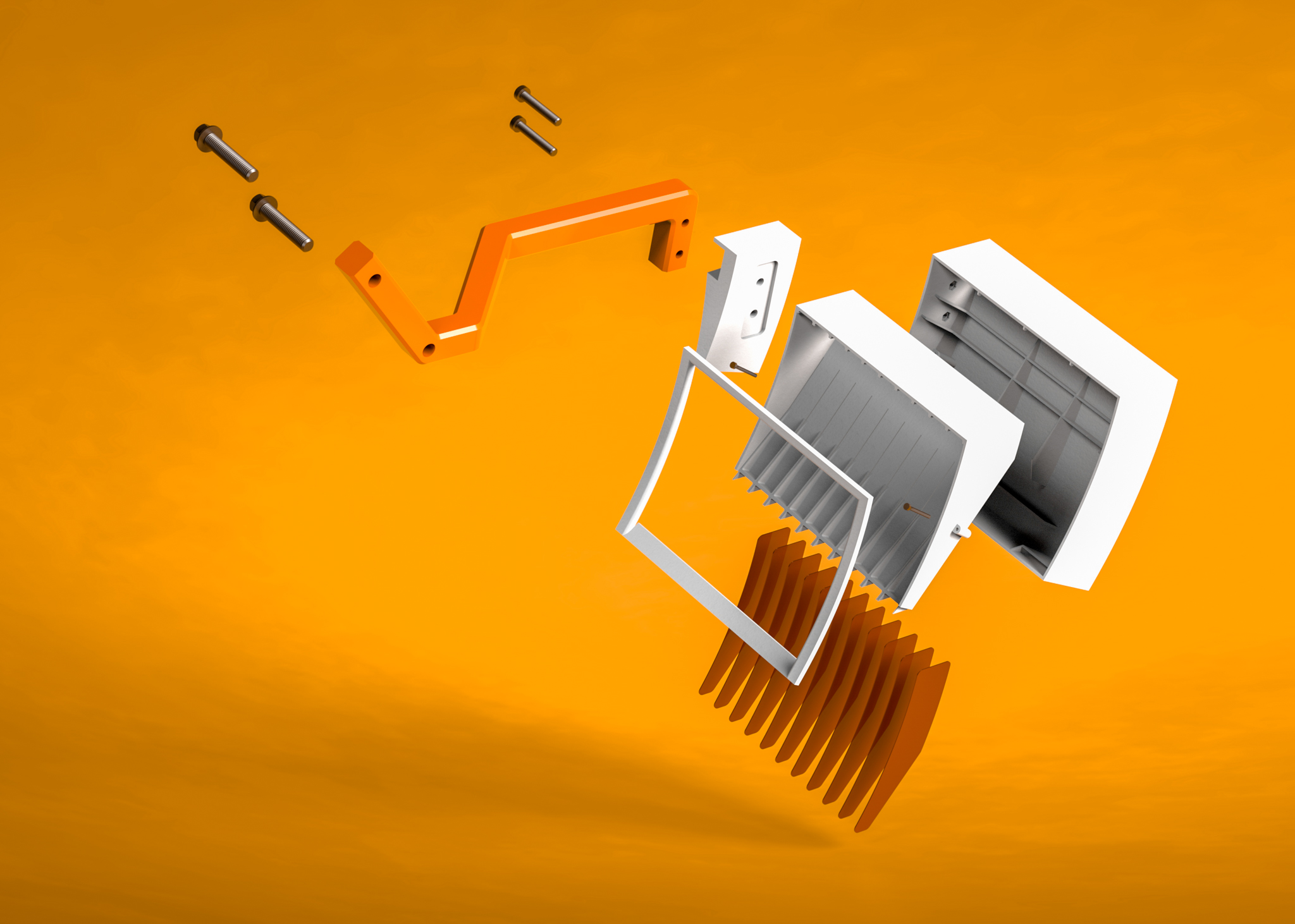
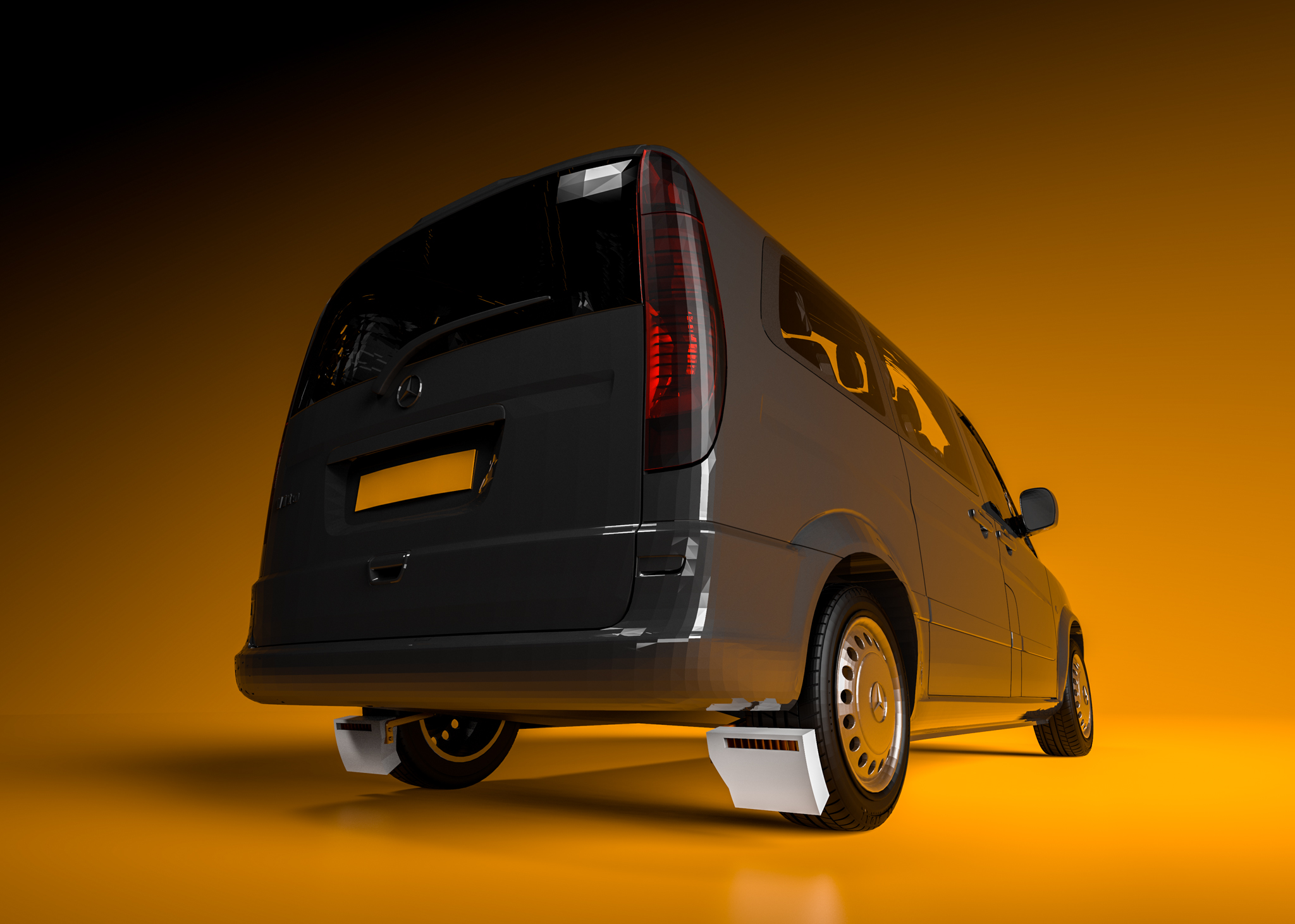


Fig. 3-7 TRAP’s design has considered DFMA practices, and is mounted to the steering knuckle - free to move with the suspension
TRAP uses electrostatics to capture charged tyre particles at source, on the vehicles themselves. Positioned close to the tyre, it prevents these harmful particles entering the wider environment. Once captured, they can be processed and reused in a variety of applications from new tyre production to inks and dyes, creating a closed loop system.
This prototype has been developed as a retrofittable solution for light commercial vehicles, dominated by logistics, booming during COVID-19. Delivery fleets have shown strong green commitments, pledging to be fully electric by 2030. Their routes are focused around cities whilst providing the regular maintenance required to empty TRAP.

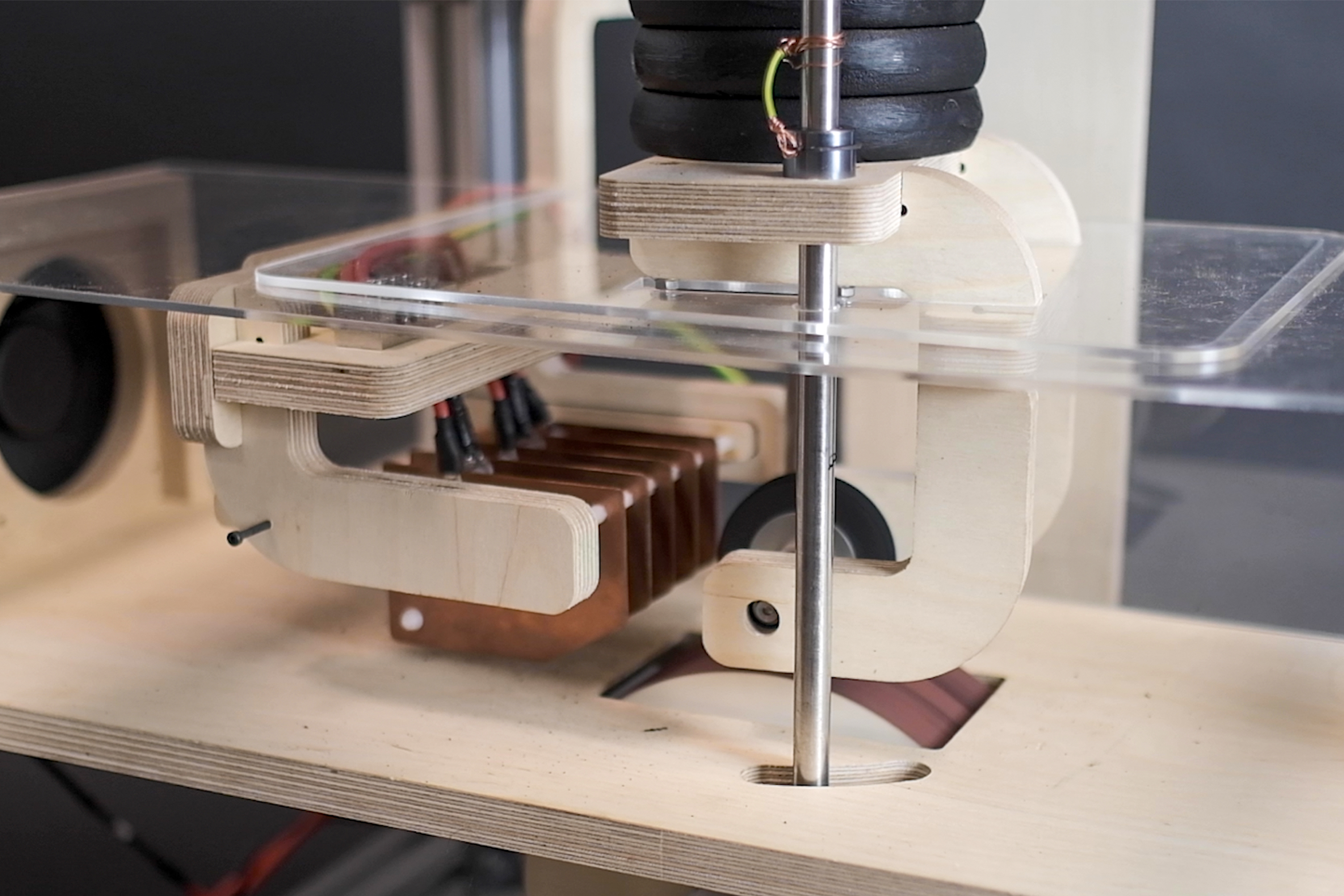


Fig. 8-12 I built a series of test rigs to better understand the key variables at play that effect capture efficiency - a sensing suite allows us to monitor test conditions
Alongside building and testing, I developed computer models to study the behaviour of charged particles under aerodynamic, electrostatic, and gravitational forces. The power of this approach is that I can run all the same experiments, that took months of physical testing, in a matter of minutes. This flexibility means trends quickly appear and new theories tested without the need to build.
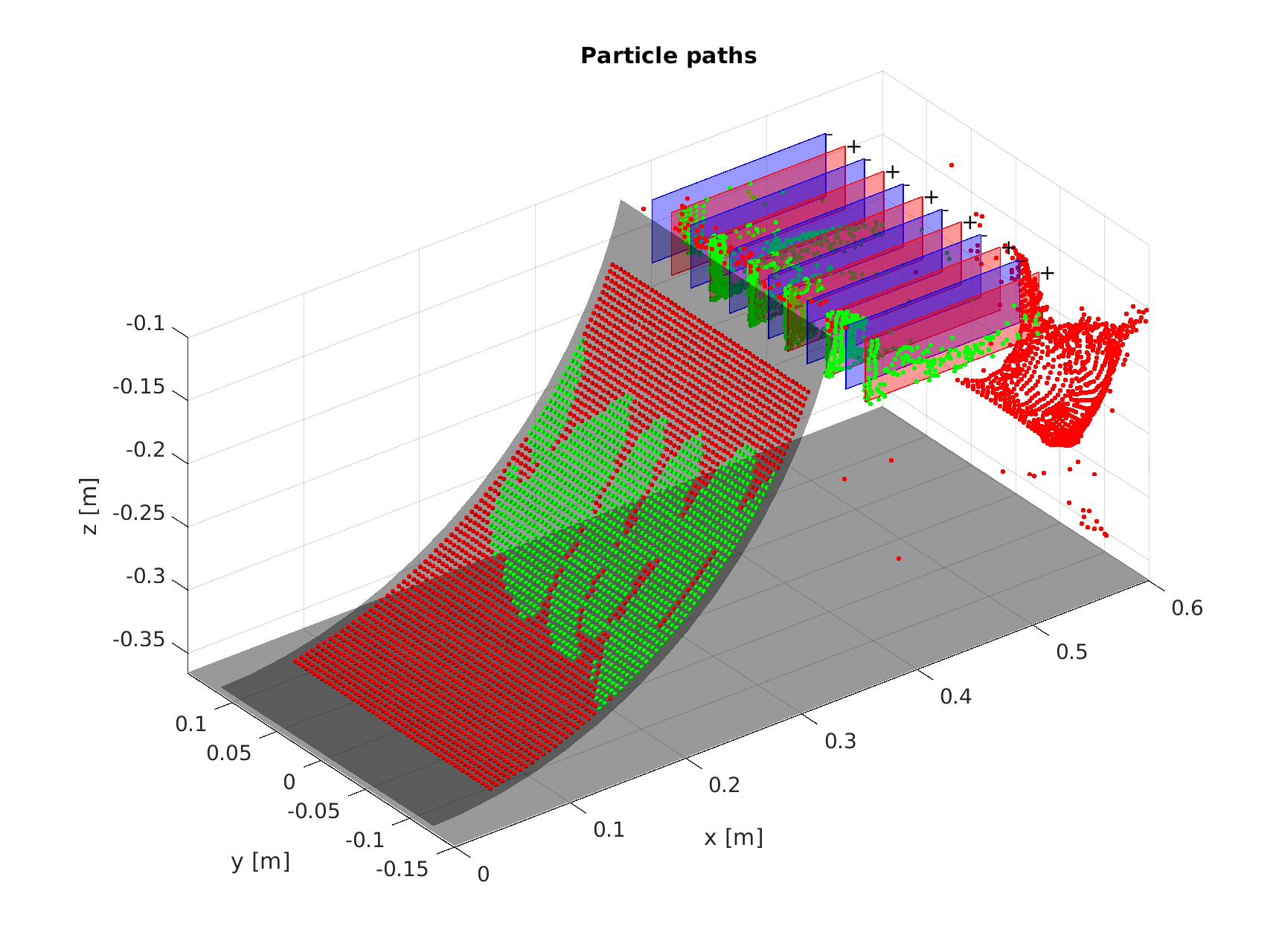
Fig. 13 A MATLAB model predicts the trajectory of the charged particles under aerodynamic, electrostatic & gravitational forces
Prototyping during a global pandemic has required every bit of ingenuity I possess, the final build was no different. Over the past 3 months, I have relied heavily on easily accessible and machinable materials. I had to cycle between six different locations regularly: two makerspaces, three professional workshops, a test facility in Hertford, and a part time framing job giving me access to a CNC.
On a personal level, this project has made me fall back in love with the engineering practice that I have so often tried to distance myself. It has been the culmination of all my years of learning - lying at the intersection of design and engineering
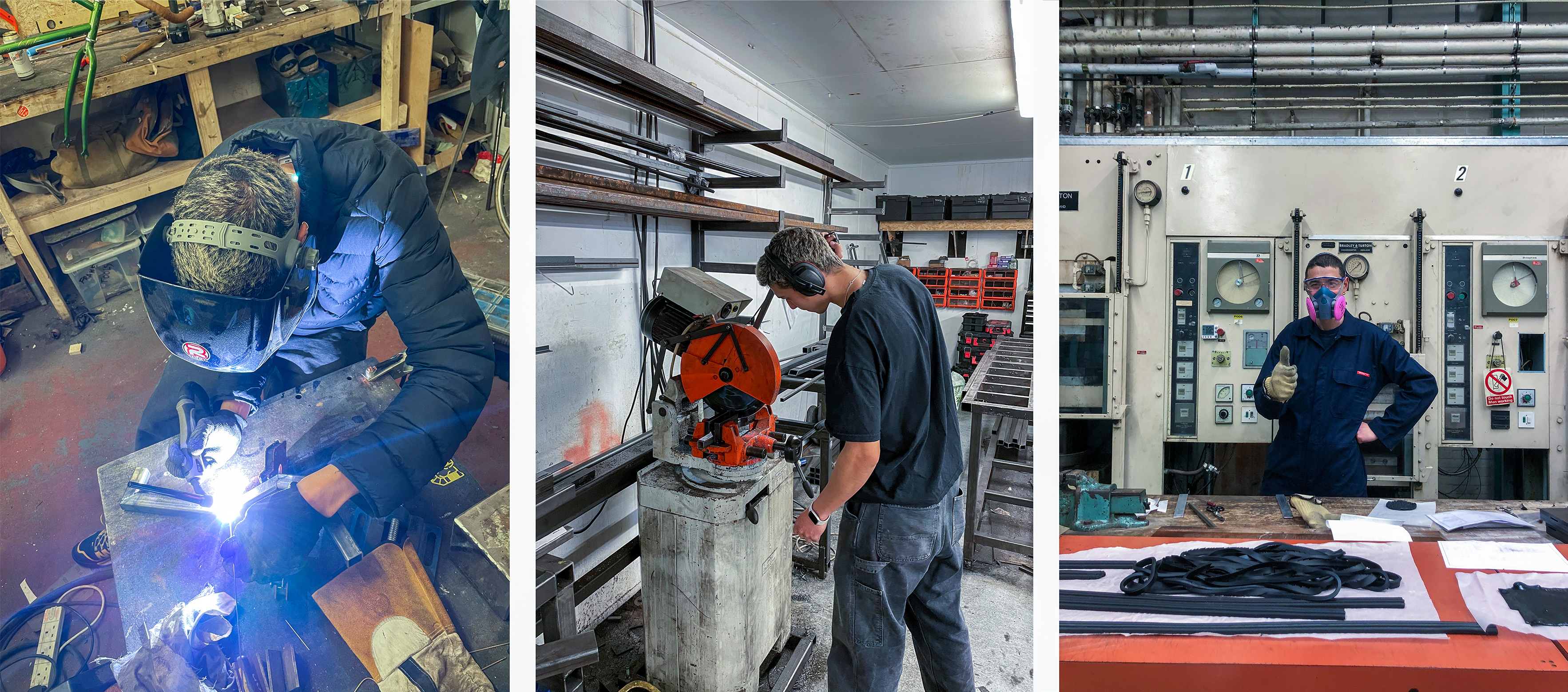
Fig. 14 Building in a national lockdown has been a challenge, I have had to cycle between 6 different workshops regularly to access all the machinery I need
Exhibitions
London Design Biennale (2021)
Dutch Design Week (2020)
Imperial Tech Foresight 2040: Moral Machines (2020)
Royal Commission of 1851, Exhibition Road Festival (2020)